Sorry for the distraction Stig.
Silent blocks come in male/male female/female and female/male.
If you use a cross brace of Aluminium strip at the front and similar at the back. Glue it to the sheet of Carbon with hot glue, then use it he appropriate silent blocks. From underneath use a large plastic washer and pan head screws. This should allow any vibration load on the Carbon sheet to be dispersed and your sheet won't crack. Increase surface area, disperse load.
The inherent problem with the Aluminium rear subframes is vibration cracking, it is doomed to fail at a certain number a cycles, and that's with the ecu mounted at the front. They were an expendable race part, like floating discs and engine cases. It's made of alley heat treated to T6, so it's hard and strong, but not overly flexible. So the less load you put on it the longer it will last. The further forward of any mass is also the better. I made a cradle for my amplifiers and moved them forward for this reason.
Think of a vibration as a pendulum. A silent block slows the movement of the weight down. So the structure move left say, a bit later the load moves left, but by this time the structure has moved back right. The effect is the load has not fully pushed on the structure and cancelled out. Or in the case of direction change only the load take longer to act so it's force is reduced. Rubber mallet Vs. steel hammer type thing.
I made my own cf tray with ribs and stiffners built it so the whole thing is brace to reduce the subframe flex. Then every thing is silent block mounted. Note the 2 thin rear silent block mounts for the amplifiers. 8000km over our roads. My chain and sprockets are worn and I chewed out a set of floating front discs from giving it some. The only casualty is the new fuse box which snapped early on in the piece. I didn't leave enough slack in the wiring loom.
It is worth having a serious think about. Racing is harsh on everything.
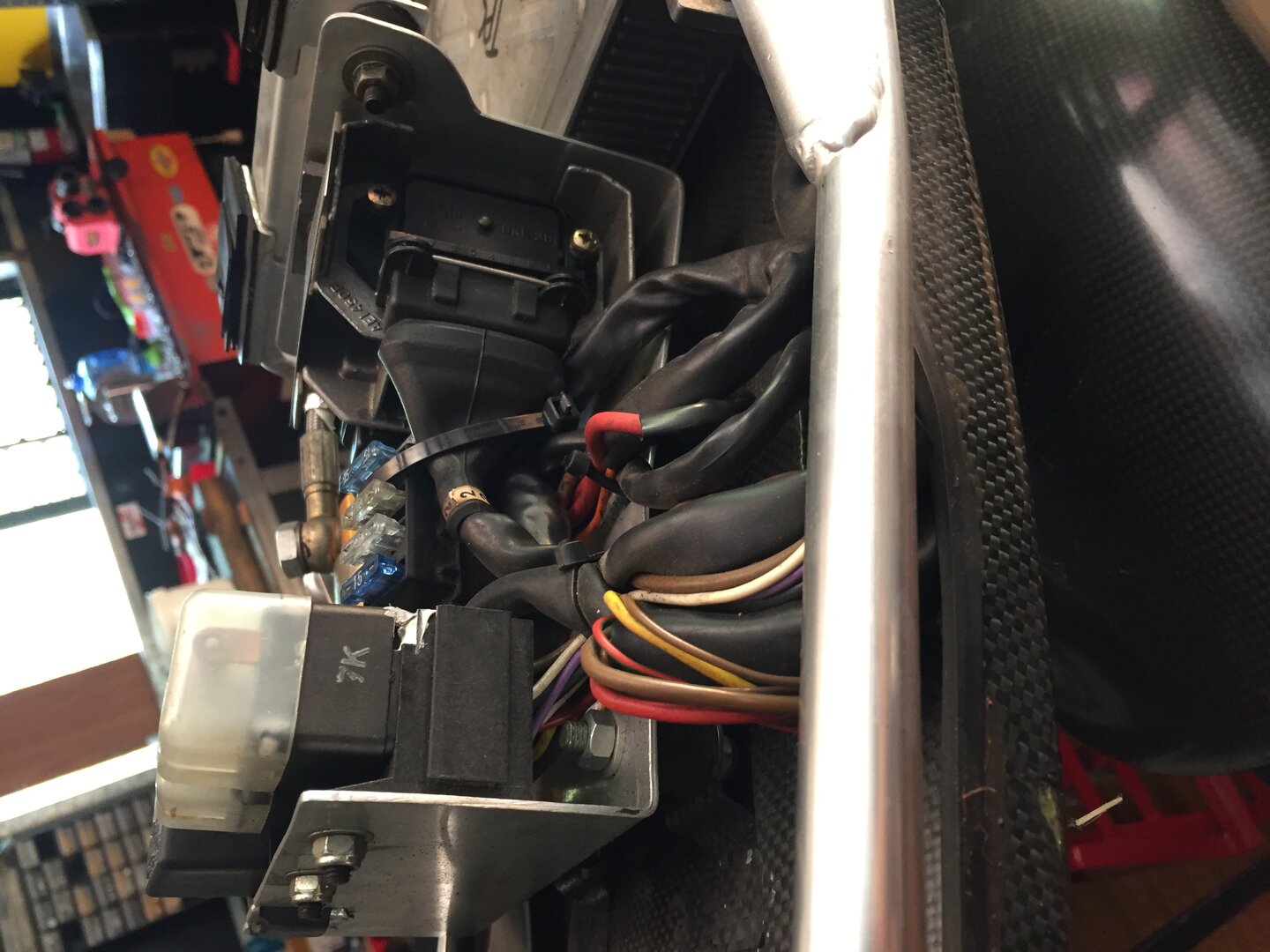
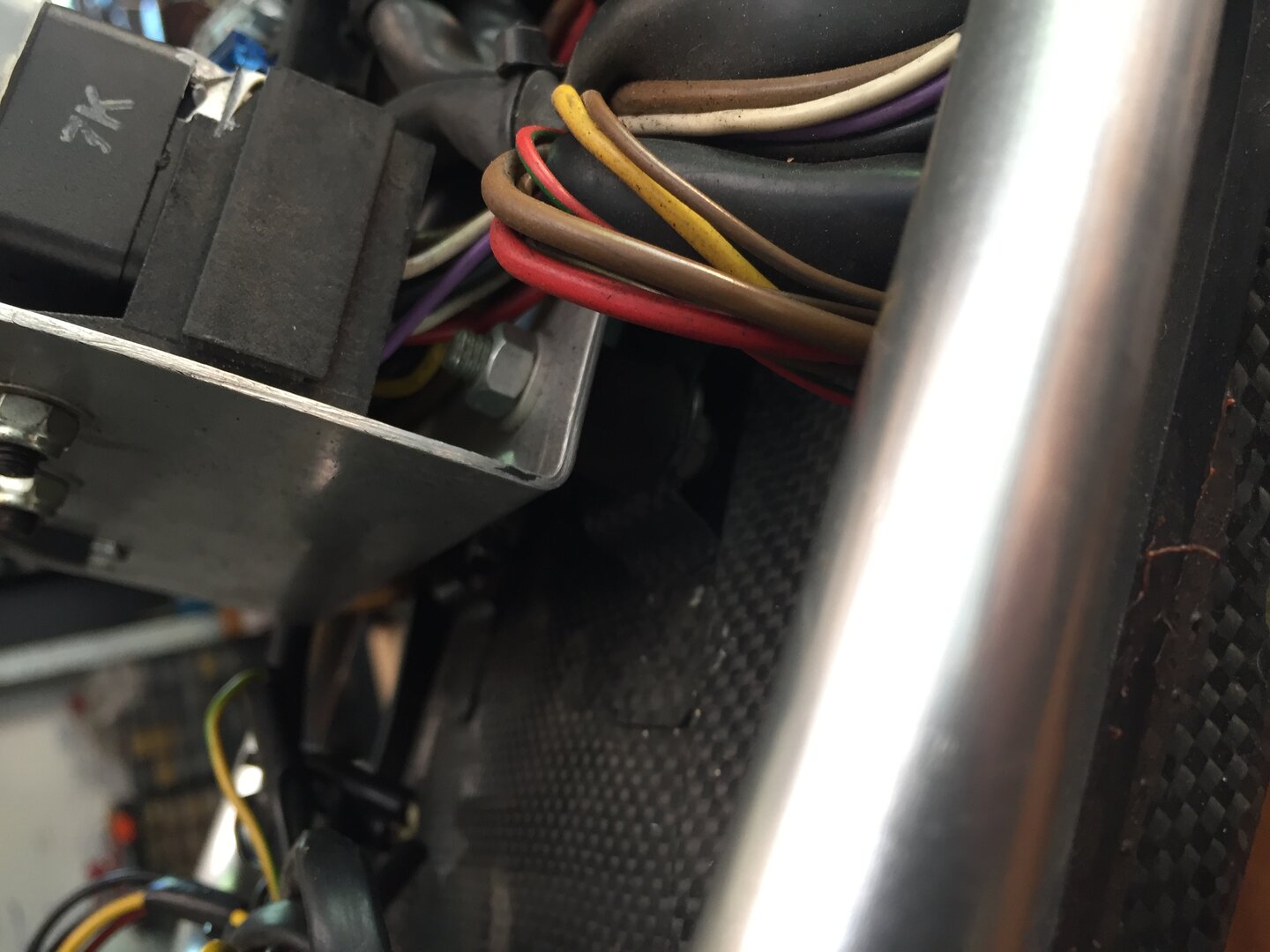
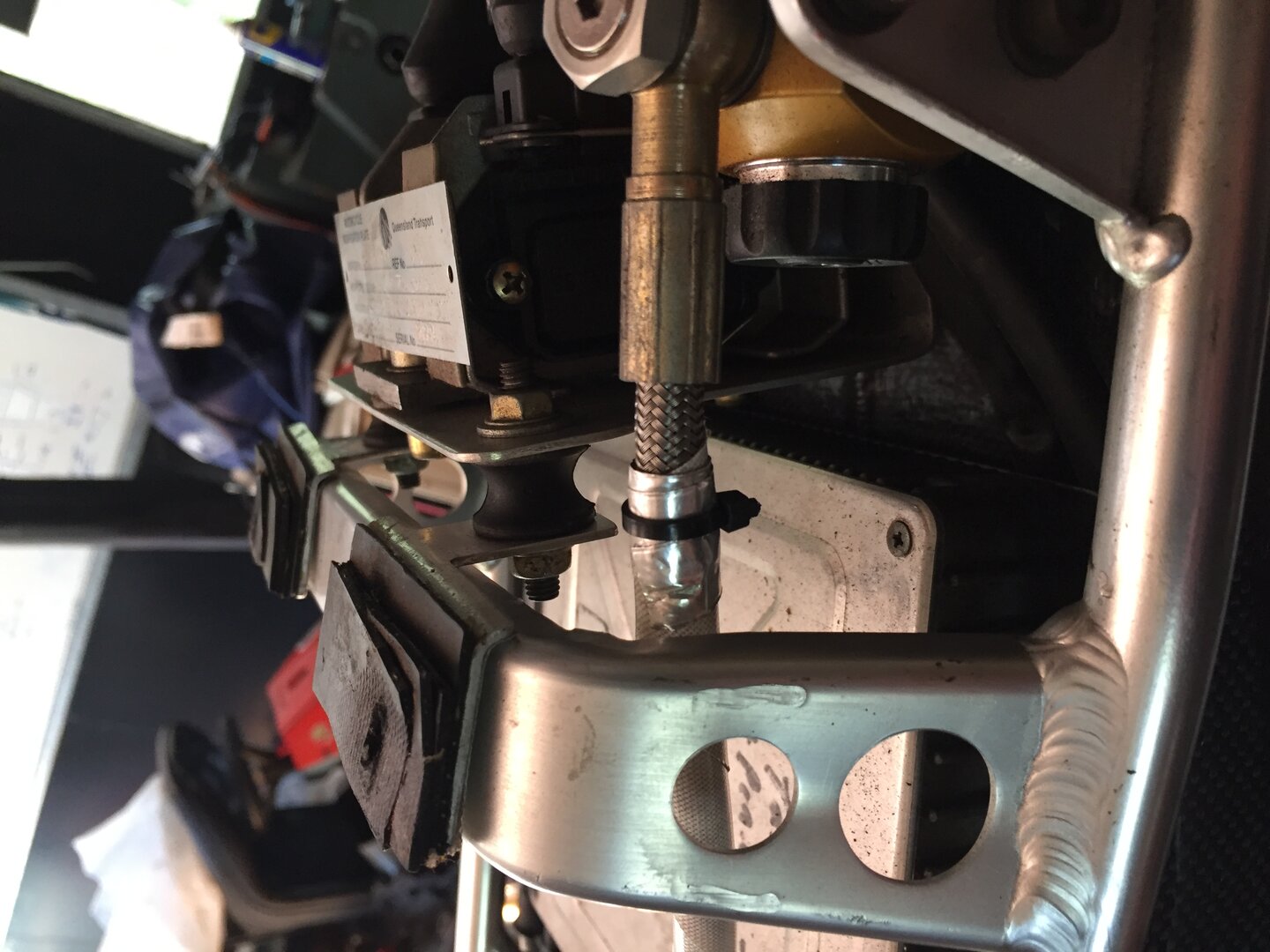
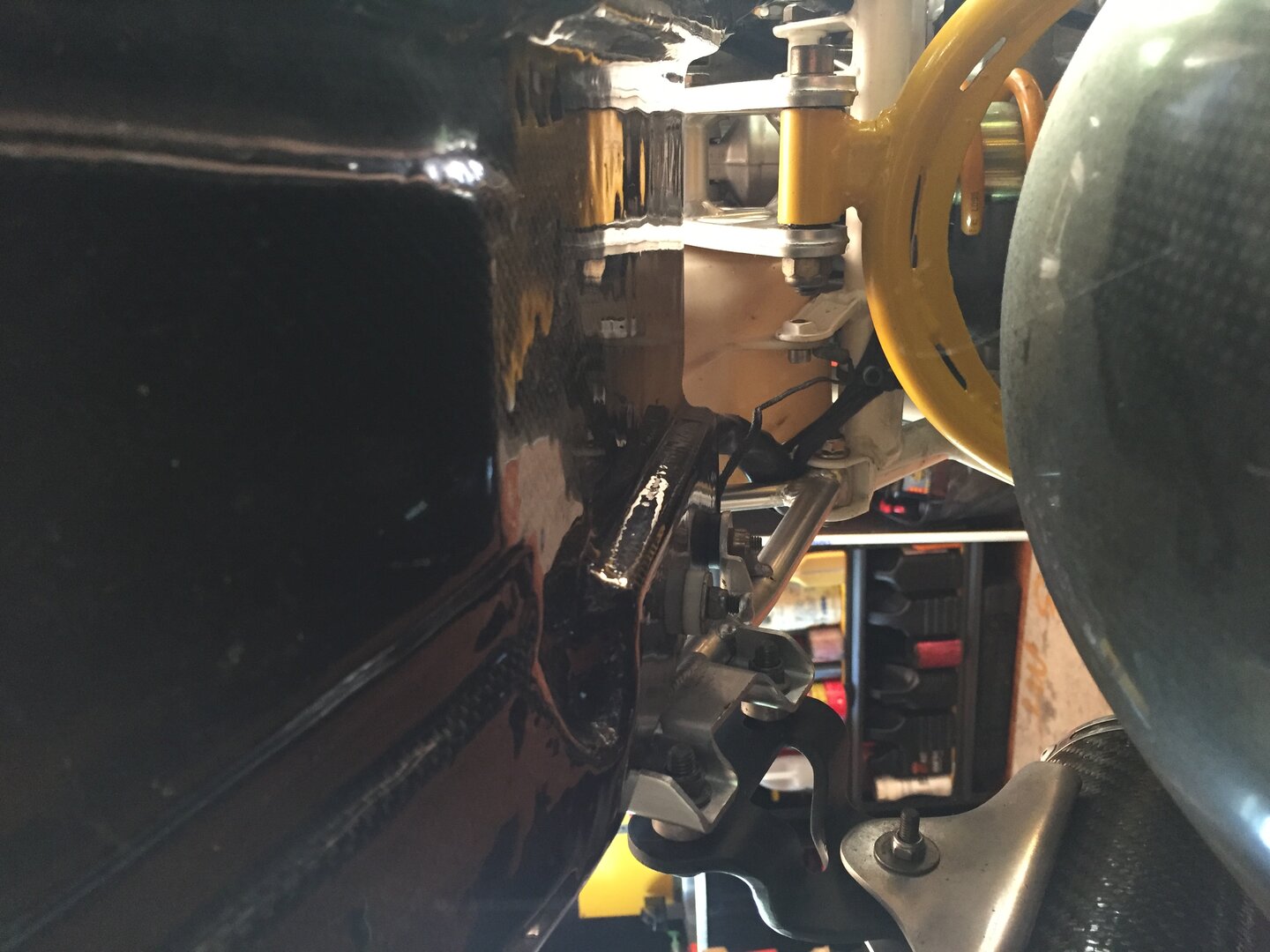