Well
Ah, along by time ago a bloke had an idea to use a system invented apparently by our German mates. When new it is remarkable to a point. That point being an RPM number. The bevel twins being 8-9k for the big bores, 10ish on the 750's, 12-13 Pantah based things and 16k for panigale. Singles about 10-11k.
So after living the definition of madness, repeat the same thing over and over again expecting a different result. I decided to change tact.
The difference between a Panigale and a single is huge in development. So what did our Italian mates do to get successful high rpm. Removed vibration, through amazing machining tolerances, ubeaut materials and design change.
A 6202 in a single has 5-7 microns tolerance, there's a few more on the rocker pivoting bits. There's 0.01-,0.03 on the closers, openers 0.10-0.15mm, the cam lobes resemble the Pyrenees. At 13000 rpm that cacophony that is the feel of an old machine, becomes a convention centre of jack hammer operators testing new equipment. And the death knell of the valve system.
I did some math stuff and due to the pathetically small contact area of an 8mm half ring, the force as you approach 12000 rpm rapidly approaches the yield point of 214N. By 13000 your in rivet gun domain, and the valve groove doesn't stand a chance. (4 sets of valves and 2 pistons and 2 con rods later. ( see madness definition). 😄
So back to little Italian mates. They drop valve stem size and clamp the closer on to stem ala MBP concept, except with style and even more surface area. Went Ti, because they can now really clamp onto the stem and it is light ( I tried Ti on 8mm, way too soft.). They finally made a cam lobe that is actually a flat and even surface. Made springs that don't fracture or resonate out of control and capitulated and went for the tried and true large contact area machined bearing surface of most overhead cam engines, to dampen out the wobble that is not far removed from a javelin in flight. Massimo blew there. Cbr's we're pulling 20000 rpm with valve springs, the 851 could have been a very serious animal. Ah if only
. Oil pressure, use oil pressure. You have heaps. Yeah, nah, yeah
.nah.
In the single, there's just not enough oil pressure to run plain cam bearings, so a precision roller is the next best thing. I've spent 9hrs so far on the cam lobes with 1500-2000 grit on a flat strip of steel and wd40, getting there another couple of hours should do it. I have to whip up new oversized rocker pins fitted to M5 tolerance (0.0009) and a special cam cap. Dry ice and warm allows you to do so much better fits. G&S valves UK are making me a set of custom 7mm Ti valves that take 749r/1098 collets and closer but still with a 7mm tip ($145 per set of collets and a shim. Ouch!) And springs are going back into stock. ???? You think.
But no. I'm still going to have a dampener. In 1986 Ford patented a doover thing. It sits between the rocker fork and the closer. But it wasn't actually their idea.. A friend of mine Geoff Howie made one in 1969 and stuck it in his single. He said it was so smooth the bike lost soul. 😁 Geoff was Marco Lucchinelli's spanner in 1975/76. (He still has the broken gear lever, they nearly got in a punch up over lightning holes drilled in it. Marco should have listened. Cost him The French round and Geoff walked 😁 )
However the doover never lasted long as it used the softness of Aluminium to sacrificially soak up the bumps.
Another mate had a think, not knowing about Ford or Geoff, and using the magic of polyurethane, gave me a really crap concept drawing which I have now made into a prototype. It is beautiful in its simplicity. Of coarse it does present some friction issues, but DLC coating will according to the maths will pretty much solve the zero running clearance for the whole desmo system.
The green box thing the head is sitting on, is actually a vibration testing bit of kit. It's got old sensors that still work sitting underneath a plate of 12mm steel sitting on springs. I can get an electric motor that spins out to 7000rpm. However when I fire it up, it will be remotely. Don't fancy a steel shaft spinning at 7k letting go and end up hanging out of my eye socket. (Age gives you wisdom😁 )
So yes Steve, the good old bearing do suffice, but I got breathing and still developing power at 14600 rpm out of the 250 before the cam nut overcame the lock washer and loctite, and had its threads stripped out. As well as a set of valves. I can't give in. My brief was make the fasted narrow case possible and blow the doors off Bultaco's !
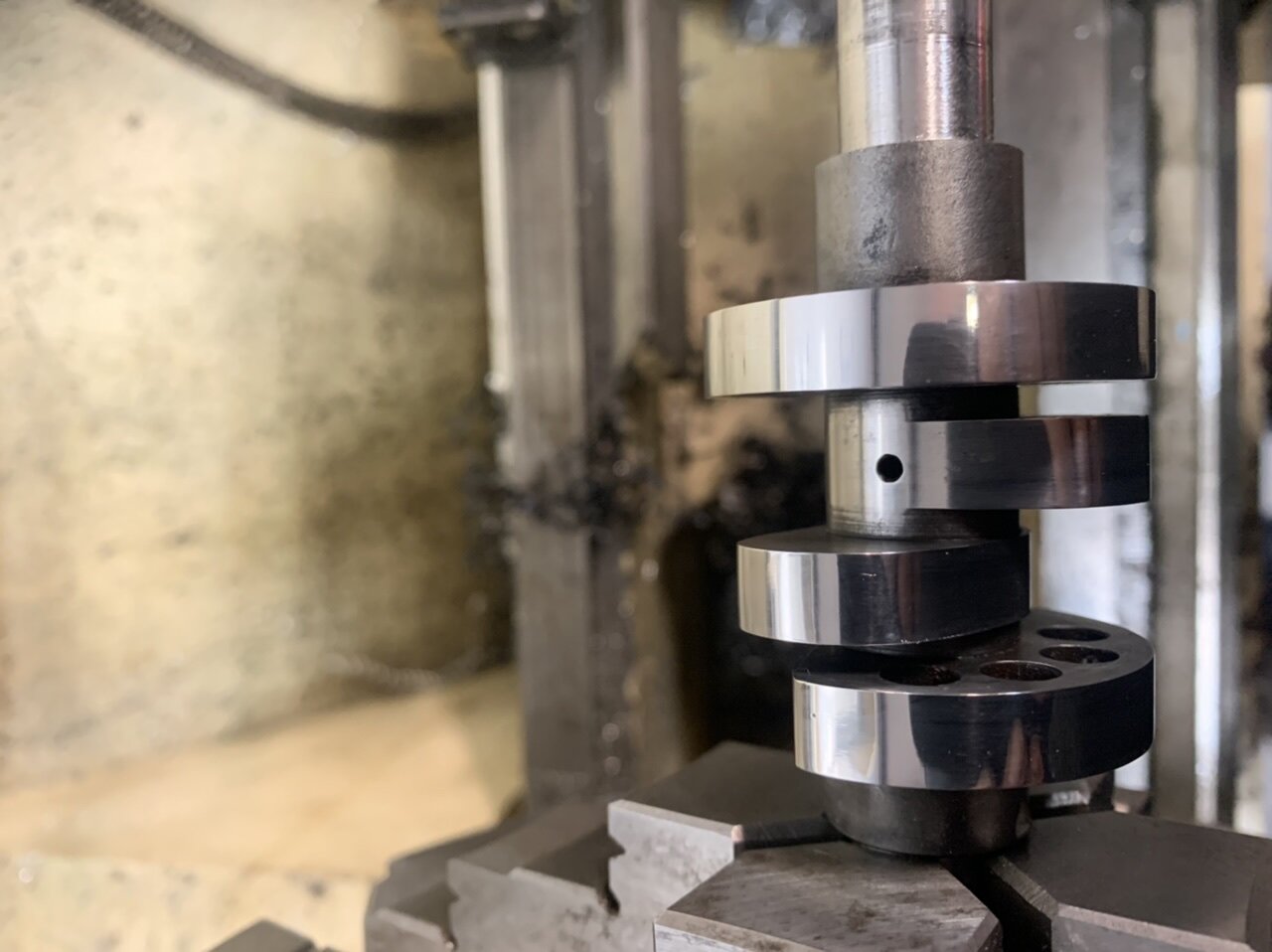
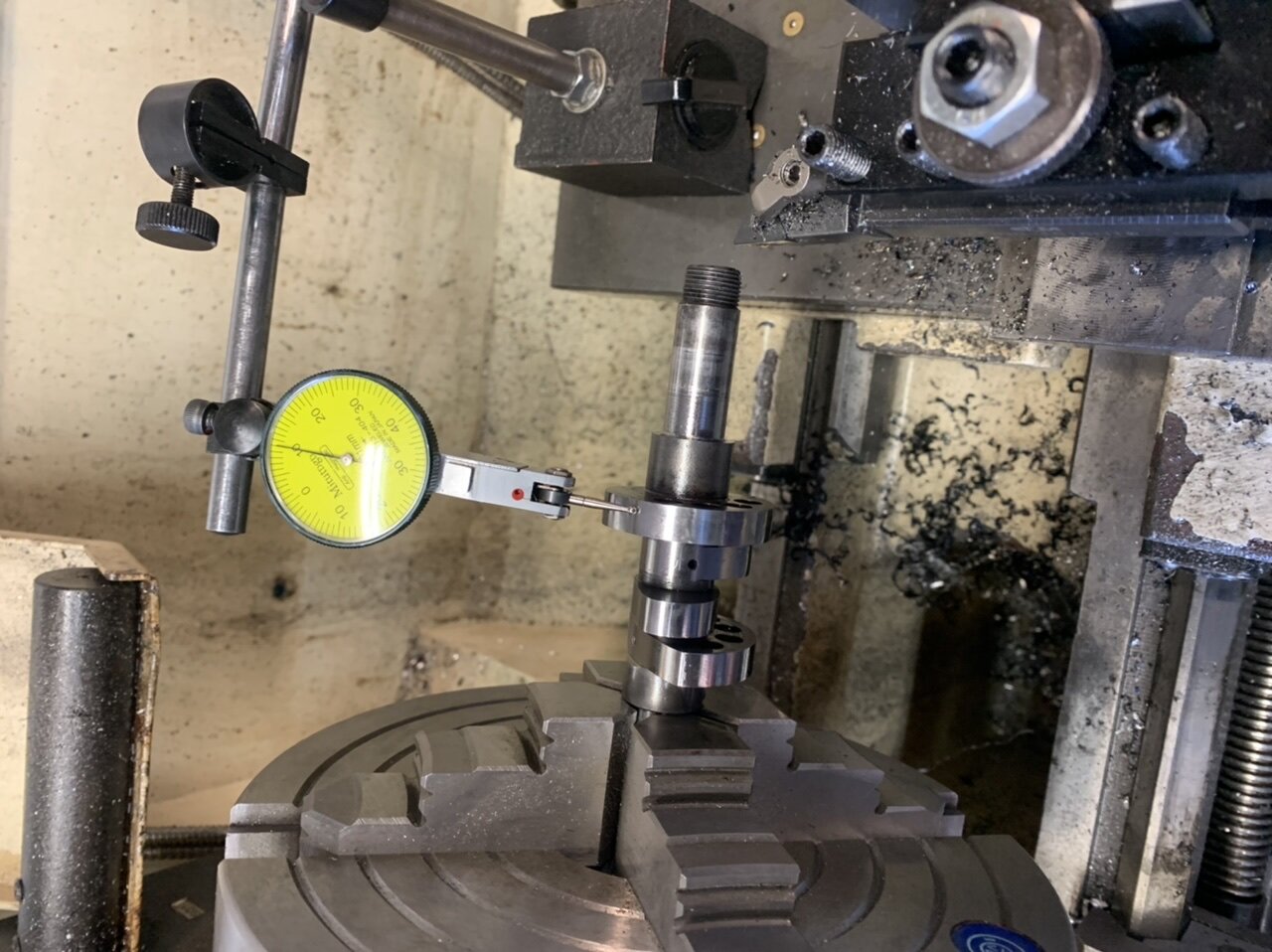
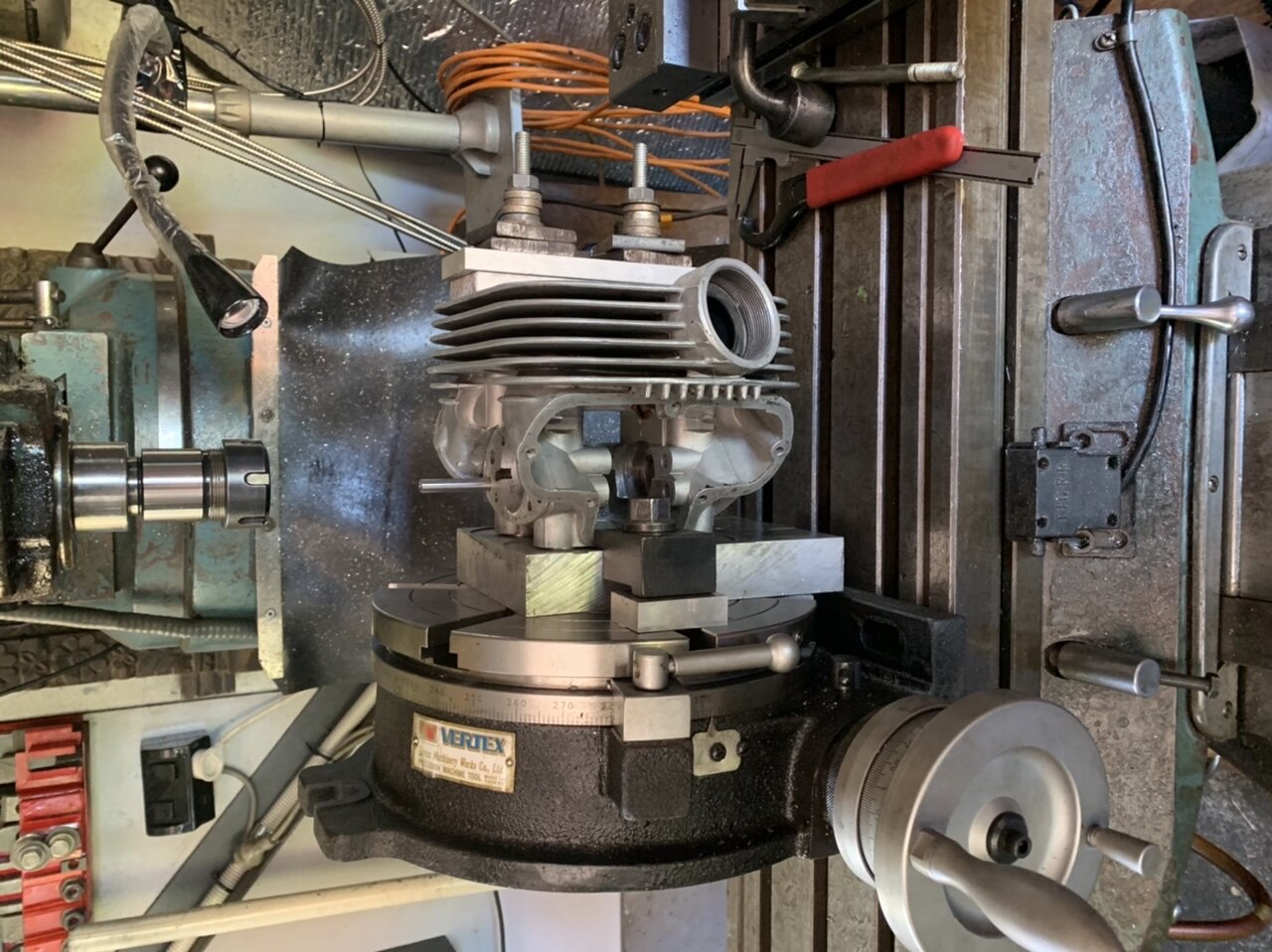