The secret is in the sealing or so they say. Well having just obtained some Pistal HC for a bevel engine I thought might as well have an in-depth look at the whole show. So armed with and instruction sheet with some numbers on it, I checked out the thermal expansion rates of the bore (cast iron sleeve in this case) the pistons ( game for new players there) and the rings. Armed with a material expansion rate calculator and he correct materials identified, of I went. Sae 4062 aluminium alloy forged and Sae 2618 aluminium forged are generally used these day, with each manufacturer having their own secret formula, but for expansion purposes they basically fall into these 2 categories.
4062 for street as it doesn’t expand as much at 106° as 2618, there by not making suspicious knocking noises on start up. Where as 2618 requires big bore clearances to allow for expansion so they knock a bit. Why 2 types, racing a WOT has different demands on a piston as opposed to going to the shop or cafe.
So after discussions with old school guys about how you do actually need 0.09 bore clearance on 2618 pistons buy using expansion calculator and cross referencing information readily available with a google search, I moved on to rings.
A ring is a length of material, the Pistals have 3 different ring materials. Funnily enough they also have 3 different sets of ring tolerances. So doing the maths, it turns out that at 106°-110°C if you set up correctly your ring will be a perfect fit just making contact with its ends, and thereby getting a perfect seal. Which of coarse is gone after 3-4000km on cast iron, but not Niklsil.
So having used the good old ring gap tool, and even once or twice yonks ago jewlers files, I decided they really aren’t up to scratch. The grinding discs are way too coarse. So this weekend I built my own using a 360 grit diamond lapping disc. (Might get a 600 grit if I have another major anal retention attack. It has N52 magnets imbedded in the base to stop the ring moving around and hold against the plate,pins,and lapping wheel.made from 6061 plate to last a lifetime. I did go overboard with the hardened 4130 shafts running in PB1 bronze bushes, but hey it was fun to make. The results were brilliant, easy to work out how many revolutions removed how much material and perfectly mating surfaces that are actually square.
Attached is the “Binky Dynamics” Mk2 precision ringing gap filing tool. Built to 0.01-0.015mm tolerances. Soon it will have a bolt on valve shim grinding attachment. Woo hoo!

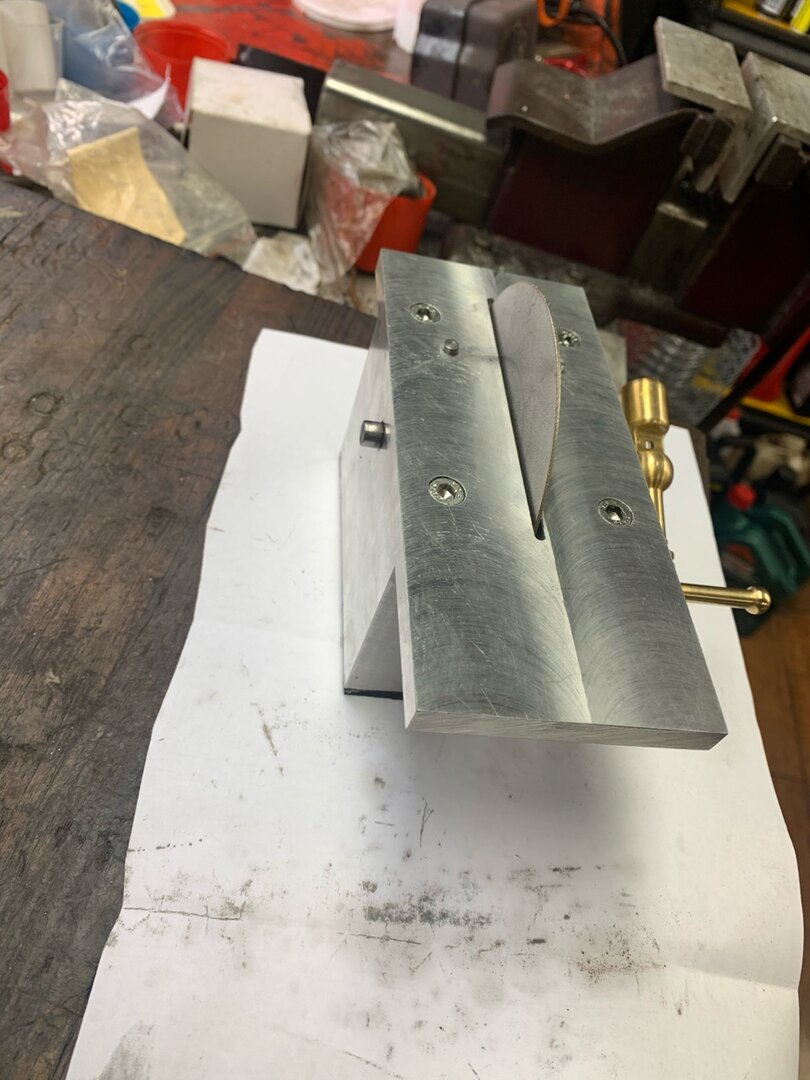