Wow. Ok so l looked at all the specs (azom.com, Atlas steel, Interalloy, bohler etc). 4340 hardened and tempered I decided was the best choice based on safety factor, and they make truck axles out of the stuff. Automotive requires a minimum of a safety factor of 3. A bike can only pull up at about .88g before the tire breaks traction on the front wheel. Front and rear is about .96g. For the front that works out at about -8.6m/sec2.
F=MA so add bike mass + rider and gear multiplied by 8.6 to give you how much load is on the axle. The suspension works on a different plane and is heaps less so I didn’t bother adding is vector in. I ended up with 2242n force, multiplied by 3 for safety factor 6756n which is about 1500lbs, 10ish megapascals. Tensile strength is the point of total failure snapped axle. Yield strength is the point the material won’t return to its original shape, bent axle. The other important one is shear, if you’ve ever seen a bent axle you realise that little crease the bearing makes is the result of a shear load. Shear is measured on a 1.27mm-12mm (0.05” to 0.5”) sample. Great hey, so how do you work out a safe wall thickness? In short, I looked at my two hollow axles, both 20mm with a 9.2mm hole. Somebody at the factory thinks 5.4mm wall thickness will do the job. I looked at some mechanical engineering forums (wow, there are some serious nerds out there, that really need to get out more), trying to get a bead on the whole load dispersal thing, too hard.
So armed with a plan, I then found out 25mm 4340 is virtually unobtainable here, and the only off cut I could find was 45mm. It took all day doing tiny cuts on my1.5 hp lathe to get down to 22/20mm. 4340 is tough stuff. I bored an 8mm hole and reamed it (I build my own valve guides) and cut the thread, then removed all the machining marks. A slide fit is 0.01mm clearance, so I took the main body down to 19.95mm ready for electroless nickel plating (corrosion protection and stinky death hard, not cheap at a tad more than hard chrome ) which will bring it back to 19.98mm.
Below are some figures. They are comparable with most sites. Would I use a hollow 7075 or Ti axle on the road. No. Fatigue would concern me and lower shear numbers. On the track, sure, but only on the track. The number of tire changes gives you many more inspection chances
Ti6al4v: shear 40Gpa-Tensile 950 mpa- yield 880mpa
Ti 3al-2.5V: shear 44Gpa-Tensile 790 mpa- yield 690mpa
4340 H&T: shear 80Gpa-Tensile 1000-1150 mpa- yield 830mpa
4140 H&T:shear 80Gpa-Tensile 930-1080 mpa- yield 740
7075 T6 shear 331 Mpa-Tensile 572 mpa - yield 503mpa
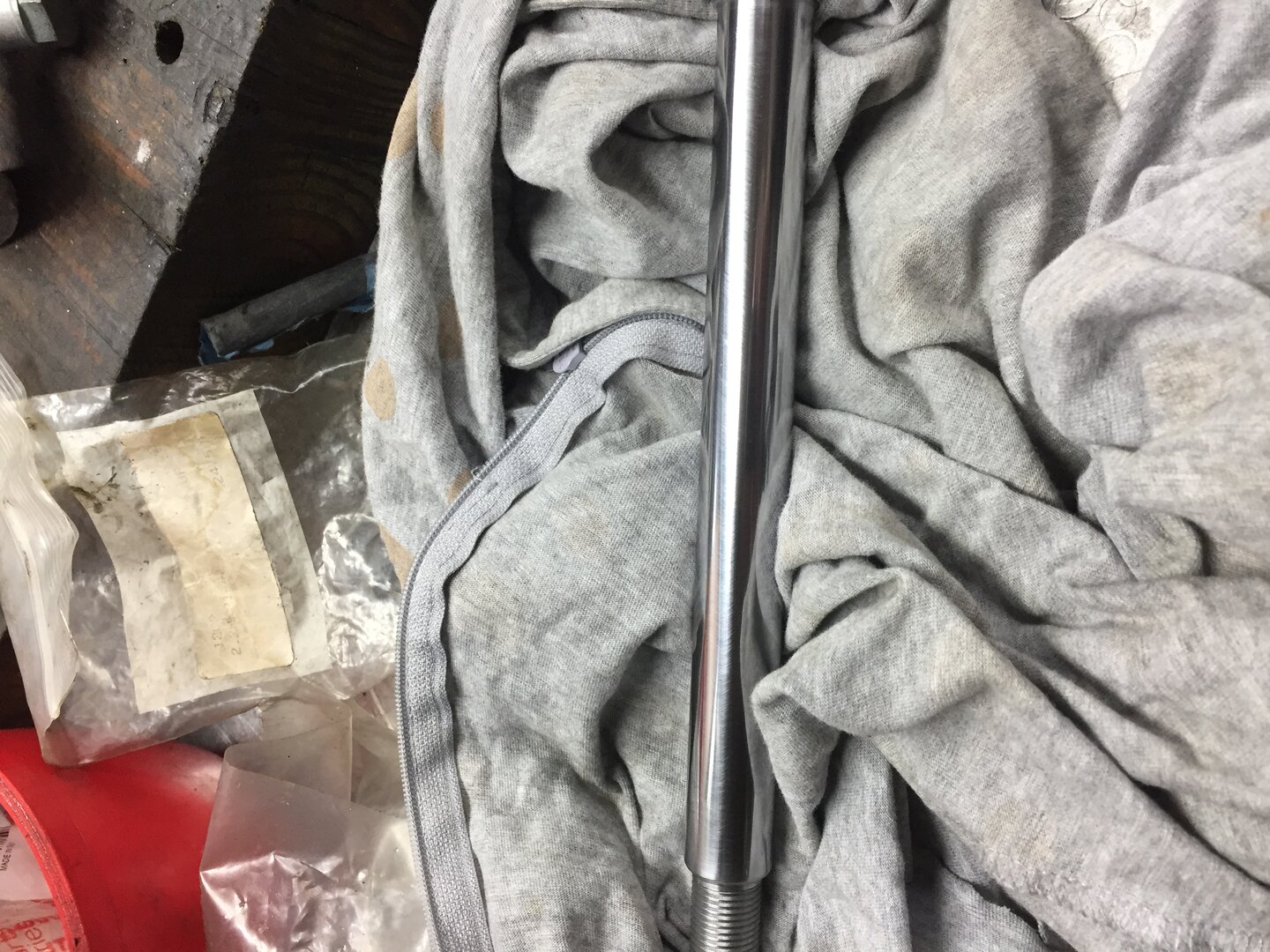